The Clear-cut Manual on Light Weight Aluminum Spreading Provider
Within the intricate globe of aluminum casting services lies a wealth of expertise waiting to be explored. As markets remain to demand precision and high quality, understanding the subtleties of light weight aluminum casting processes comes to be extremely important. From the important devices and devices to the crucial facet of quality assurance, every information plays a significant function fit the last outcome. However, what genuinely sets an extensive handbook apart is its capability to not just supply foundational expertise but additionally to supply insights right into taking full advantage of effectiveness and performance. As we browse with this clear-cut handbook, uncovering market patterns and technologies that form the landscape of light weight aluminum casting services, we are advised of the unlimited opportunities that await those happy to submerse themselves in this complex craft.

Recognizing Aluminum Casting Procedures
Exploring the ins and outs of aluminum spreading procedures reveals the precision and intricacy involved in transforming liquified metal right into detailed components - casting aluminum. Light weight aluminum spreading is a thorough manufacturing method that includes the pouring of liquified light weight aluminum right into a mold and mildew to create a wanted form. This procedure begins with the thorough preparation of the mold, which need to be crafted with accuracy to ensure the end product's accuracy. As soon as the mold and mildew is ready, the aluminum is warmed to its melting factor and poured right into the mold and mildew tooth cavity.
Throughout the cooling procedure, the light weight aluminum takes the shape and strengthens of the mold. What complies with is precise workmanship to remove any imperfections and improve the part to meet the needed specifications. This procedure demands a keen eye for information and a deep understanding of metallurgy to make sure the last product's top quality and stability.
Comprehending the subtleties of aluminum casting processes is crucial for creating high-quality parts that satisfy market criteria and needs. From aerospace to auto sectors, the precision of light weight aluminum spreading plays a vital function in making trusted and durable parts.
Essential Devices and Equipment
What devices and tools are indispensable for attaining accuracy and performance in aluminum casting processes? To ensure effective aluminum spreading, numerous necessary tools and tools are required. By making use of these tools and tools effectively, light weight aluminum spreading solutions can achieve high accuracy and efficiency in their processes.
Quality Assurance in Aluminum Casting
Ensuring constant quality requirements is paramount in light weight aluminum casting processes to fulfill market requirements and customer expectations. Quality control in light weight aluminum spreading involves a systematic method to tracking and assessing every stage of the spreading process to guarantee the end product's integrity. To accomplish this, different approaches are employed, such as aesthetic examinations, dimensional checks, non-destructive screening, and product analysis. Visual assessments are performed to identify surface flaws like fractures, porosity, or insufficient fills up. Dimensional checks make certain that the casting fulfills specific specifications. Non-destructive screening approaches like X-ray, ultrasonic, or color penetrant assessments can find internal flaws without harming the part. Product evaluation via spectroscopy or chemical testing validates the structure of the aluminum alloy used (casting aluminum). By implementing stringent quality assurance actions, light weight aluminum casting company can supply parts that adhere to the highest criteria of performance, quality, and dependability, ultimately satisfying both industry laws and customer demands.
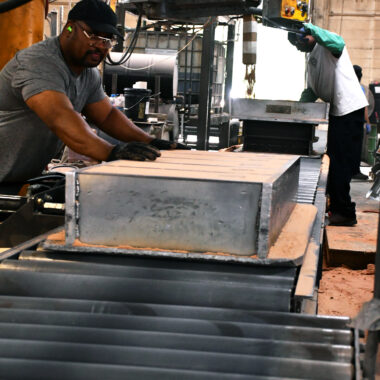
Maximizing Efficiency and Performance
To enhance operational efficiency in aluminum spreading solutions, maximizing performance and performance is important for conference production needs and preserving competitive advantage in the sector. Implementing lean production concepts, such as reducing waste and enhancing procedures, can considerably boost total effectiveness. Utilizing sophisticated modern technology, like computer-aided style (CAD) software application and automated systems, can boost productivity by reducing manual work and increasing accuracy.
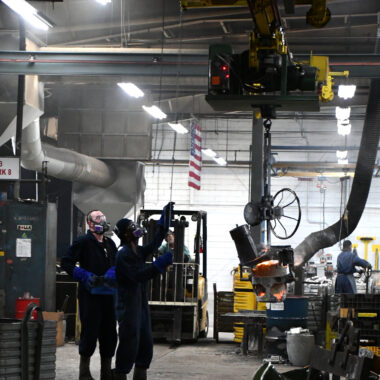
Teaming up very closely with distributors to make sure a constant circulation of high-grade materials and carrying out durable organizing and supply management systems are also vital techniques for optimizing efficiency in aluminum casting services. By concentrating on these areas, firms can attain higher levels of efficiency, satisfy client needs properly, and remain ahead in an affordable market.
Sector Fads and Advancements
In action to the developing landscape of light weight aluminum casting services, staying abreast of sector patterns and Click This Link innovations is critical for keeping an one-upmanship and satisfying the dynamic needs of the market. One significant pattern in the aluminum spreading market is the increasing focus on sustainability and ecological obligation. Companies are adopting greener practices, such as using recycled light weight aluminum and implementing energy-efficient procedures, to line up with customer assumptions and regulative requirements.
Additionally, improvements in innovation are reinventing light weight aluminum spreading procedures. The combination of automation, robotics, and expert system is streamlining manufacturing, content boosting accuracy, and lowering preparations. 3D printing is also making waves in the sector by enabling intricate geometries to be produced with greater performance and cost-effectiveness.
Additionally, there is an expanding focus on personalization and product customization. With customers seeking distinct and customized items, aluminum casting services are adapting to offer more adaptable production remedies. By embracing these industry patterns and advancements, firms can place themselves for success in a rapidly progressing market.
Final Thought
Finally, the manual on aluminum spreading solutions offers an extensive overview of the processes, devices, quality assurance measures, efficiency methods, and market patterns in the area. By recognizing these vital aspects, services can enhance their spreading procedures, ensure high-quality products, and remain affordable on the market. This definitive handbook offers as a useful resource for those involved in aluminum casting solutions.
As sectors proceed to require precision and quality, recognizing the nuances of aluminum casting processes ends up being paramount (casting aluminum). Aluminum casting is a precise production method that includes the pouring of liquified light weight aluminum into a mold and mildew to produce a desired form.Guaranteeing regular high quality requirements is paramount in aluminum spreading processes to fulfill industry requirements and client expectations. Quality control in aluminum casting involves an organized approach webpage to monitoring and examining every stage of the casting process to guarantee the final product's integrity.In final thought, the manual on light weight aluminum casting solutions gives an extensive review of the processes, devices, quality control measures, performance strategies, and market fads in the area